How a Wireless Power Monitor Can Save You Money
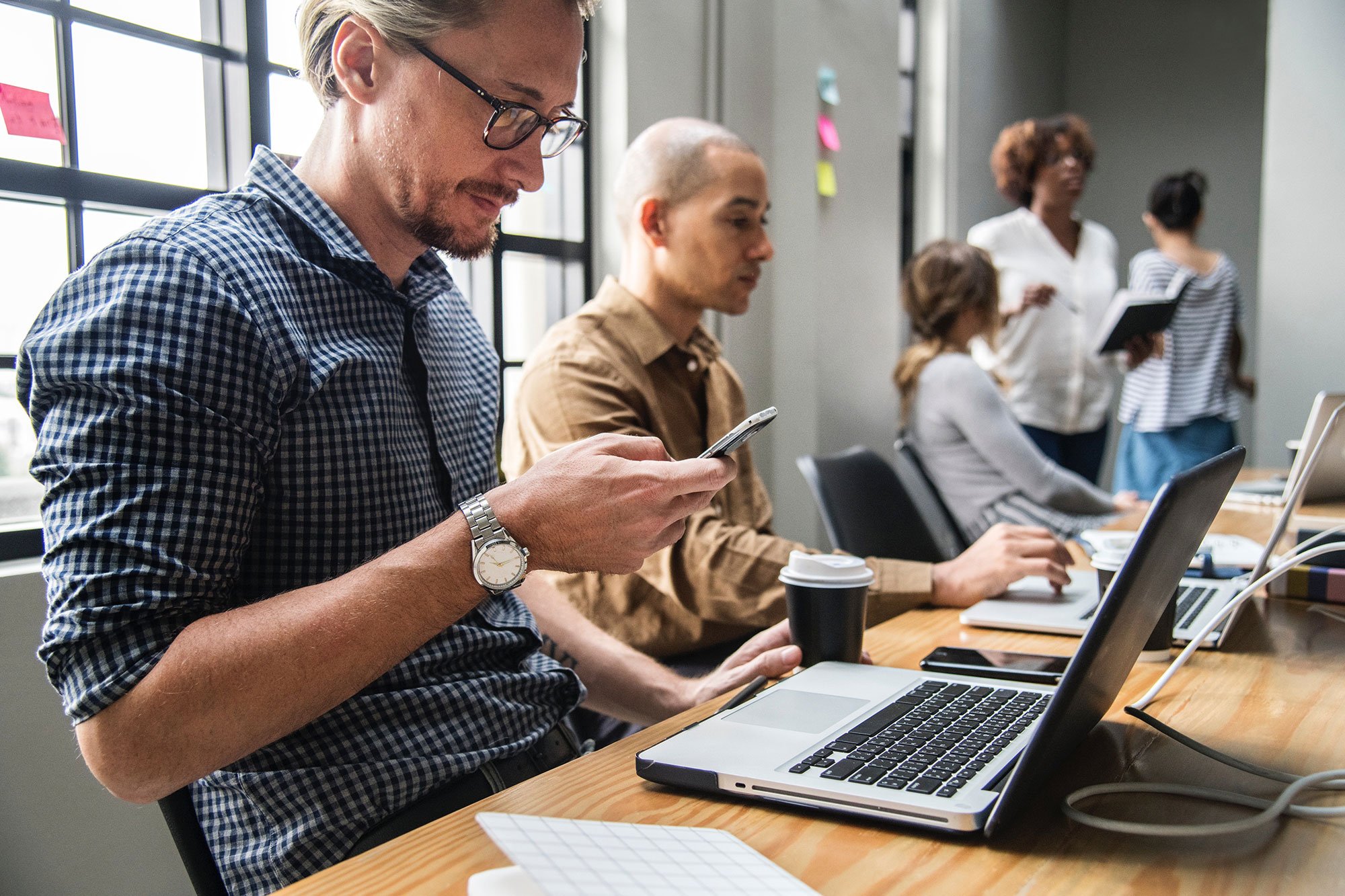
A wireless power monitor might not grab headlines, but it’s becoming one of the most practical tools for lowering energy costs. It gives businesses, property managers, and homeowners a clearer picture of how electricity is used—and where it’s wasted.
With electricity prices climbing and equipment running longer hours, knowing exactly what’s drawing power (and when) is no longer a luxury—it’s necessary. This article walks through how a wireless power monitor works, why it saves money, and how companies are quietly using it to cut costs and improve operations.
What Is a Wireless Power Monitor?
A wireless power monitor measures and tracks electricity usage without the need for complex wiring. It’s typically made up of sensors, a gateway, and software that gives you access to real-time and historical data. The data is transmitted wirelessly to a local server or cloud dashboard.
These systems are often easier to install than traditional wired monitors and work well for both new and existing buildings. Installations don’t usually require opening up walls or disrupting day-to-day operations.
Many systems, like those from Packet Power, use a type of mesh network that allows the devices to “talk” to each other. This setup helps reduce signal problems and makes it easier to expand the system later on.
Why Energy Monitoring Matters
The U.S. Department of Energy estimates that commercial buildings waste about 30% of the energy they consume. A lot of this is due to poor scheduling, outdated equipment, or just a lack of visibility.
Think of it like this: If you only look at your utility bill once a month, you’re missing out on hundreds of small decisions that add up. By the time you see the cost, the damage is done.
With a wireless power monitor, you can track what’s happening throughout the day, catch problems early, and adjust your usage before it affects your bill.
How a Wireless Power Monitor Helps You Save
1. See What’s Using the Most Power—Right Now
One of the biggest advantages is being able to see electricity usage as it happens. You can spot equipment that’s running longer than it should, find spikes in demand, and figure out which systems are using more power than expected.
Organizations that monitor energy consistently can often cut usage by 10–20%, just by making small operational changes, according to Energy Star.
2. Avoid Peak Demand Charges
For commercial and industrial buildings, utilities often charge based on your highest level of energy use in a short window, often 15 minutes. A single spike during the month can increase your entire bill.
A wireless power monitor helps manage this by showing you when peaks are happening. You can reschedule or stagger equipment usage to avoid them.
3. Catch Equipment Problems Early
Over time, failing equipment often starts using more power. A fan motor pulling extra current or a compressor cycling too frequently could be signs of mechanical problems.
A wireless monitor flags these issues early, allowing you to address them before they cause downtime or require costly emergency repairs.
4. Match Usage with Occupancy
If your HVAC or lighting systems are running full speed even when no one is around, you’re wasting money. Wireless monitoring can help identify these patterns.
In a recent study by the U.S. General Services Administration, federal buildings that paired energy monitoring with occupancy-based controls reduced energy use by up to 26%—without affecting comfort.
5. Bill Tenants (or Departments) Accurately
In multi-tenant buildings or large facilities, energy costs are often split by square footage, which isn’t always fair. A wireless power monitor allows you to bill based on actual use.
This encourages tenants to conserve energy and helps avoid billing disputes. Internally, departments or business units can be tracked the same way, creating more accountability.
Who’s Saving and How
1. Small Manufacturer in Ohio
After installing wireless monitors on its shop floor, a mid-sized manufacturer found that two compressors were running at the same time unnecessarily. By adjusting schedules and reducing redundancy, they cut energy use by 20% and saved over $18,000 annually.
2. Commercial Building in Atlanta
A property manager added wireless sub-metering to a 12-story building. Previously, tenants were billed based on square footage. With accurate data, they were able to adjust the billing method and recover more than $25,000 in previously missed charges.
3. University in California
A university noticed several lecture halls had HVAC systems running overnight. After reviewing the data from their wireless monitoring system, they updated the scheduling system. This small change helped cut electricity use during off-hours by 15%.
Cost vs. Payoff
Installing a wireless power monitor comes with some upfront costs. For a typical office or mid-sized facility, expect to spend between $5,000 and $25,000, depending on the scale.
But that investment often pays off within 6 to 18 months. That’s because savings come from multiple directions:
- Lower energy use
- Fewer equipment failures
- Avoided demand charges
- Better billing and accountability
The Lawrence Berkeley National Laboratory has found that even partial monitoring systems can lead to immediate reductions in energy use, often within the first few weeks of deployment.
Wireless vs. Wired Systems
Both types of systems can track energy use, but wireless options have some key advantages, especially in retrofit scenarios.
Why wireless makes sense:
- Easy to install without major construction
- Works well for expanding buildings or changing floor plans
- Sends data in near real-time to software dashboards
Things to consider:
- Batteries in some sensors may need occasional replacement
- Be sure the system encrypts data and uses secure protocols
Today’s wireless systems are highly reliable and built for commercial environments. Brands like Packet Power use custom mesh networks that are specifically designed for energy data—not generic Wi-Fi, which can be less stable in industrial settings.
What to Look For in a System
If you’re thinking about investing in a wireless power monitor, here are a few things to keep in mind:
- Data Accuracy: Look for high sampling rates and real-time feedback.
- Cloud Access: Make sure data is easy to access remotely.
- Integration: Choose systems that can work with your existing building automation systems.
- Scalability: Start small, but make sure the system can grow with your needs.
Top providers like Packet Power, Schneider Electric, and Siemens all offer systems that cover everything from basic load tracking to detailed analytics for large facilities.
How to Get Started
Getting started doesn’t have to be complicated. Most experts recommend a phased approach:
- Do a Simple Audit – Walk through your facility and note areas with high energy use.
- Set Goals – Know whether you’re trying to cut costs, track tenants, or prevent downtime.
- Start Small – Begin with one building or department to test the system.
- Review Data Regularly – Use the insights to change behavior and improve systems.
- Get the Team Involved – Work with facilities, finance, and IT from the start.
Conclusion
A wireless power monitor gives you the information you need to stop guessing and start managing energy more effectively. Whether you run a facility, manage a property, or simply want to reduce overhead, gaining visibility into energy use can be a smart and affordable first step.
These systems help identify waste, improve performance, and catch issues early. And in many cases, the investment pays for itself in just a few months.
Interested in learning more? Contact Packet Power to see how we can help you make better energy decisions—and save money doing i